Essential Tools for Successful Manufacturing Operations
In the fast-paced world of manufacturing, staying ahead of the competition means embracing technological advancements that streamline production and enhance quality. With the rapid evolution of industry standards and customer expectations, manufacturers must invest in a variety of tools and systems to maintain their edge. These range from automation and robotics to sophisticated software solutions capable of managing complex operations. Below, we explore the critical tools necessary for a successful manufacturing operation in the current industrial landscape.
Implementing Robust ERP Solutions for Streamlining Processes
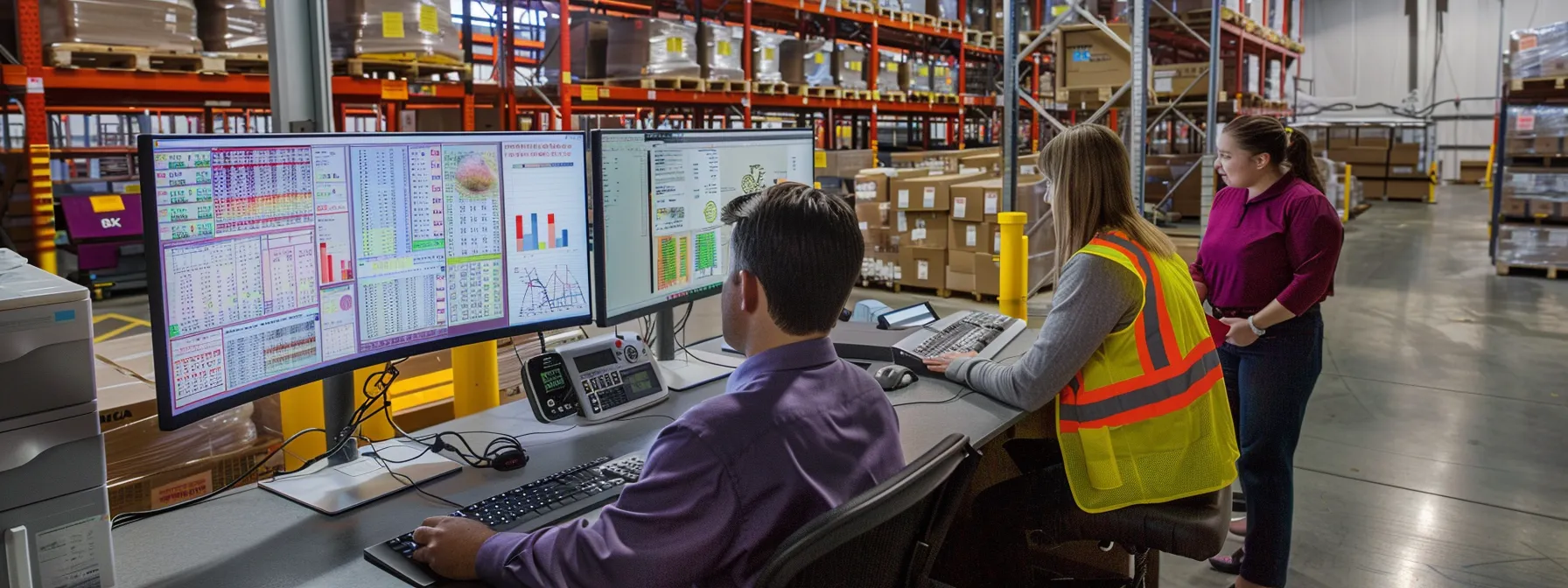
At the heart of any well-oiled manufacturing operation lies an effective Enterprise Resource Planning (ERP) system. These comprehensive solutions manage various aspects of the business, from supply chain logistics to customer relations and human resources. The right ERP system can transform sprawling, disjointed processes into a streamlined, unified operation.
An ERP not only helps manage the everyday details but also improves strategic planning by offering a bird’s-eye view of the entire operation. By centralizing data, it enables manufacturers to make more informed business decisions with greater speed and accuracy. This can translate into better use of resources, cost reductions, and more agile responses to market changes.
Integrating an ERP system often presents a challenge, but the long-term efficiency gains can be monumental. One example is the implementation of manufacturing ERP software, which can optimize production schedules, manage inventory levels, and provide invaluable insights into operational performance.
Utilizing Advanced Analytics and the Internet of Things (IoT) for Predictive Maintenance
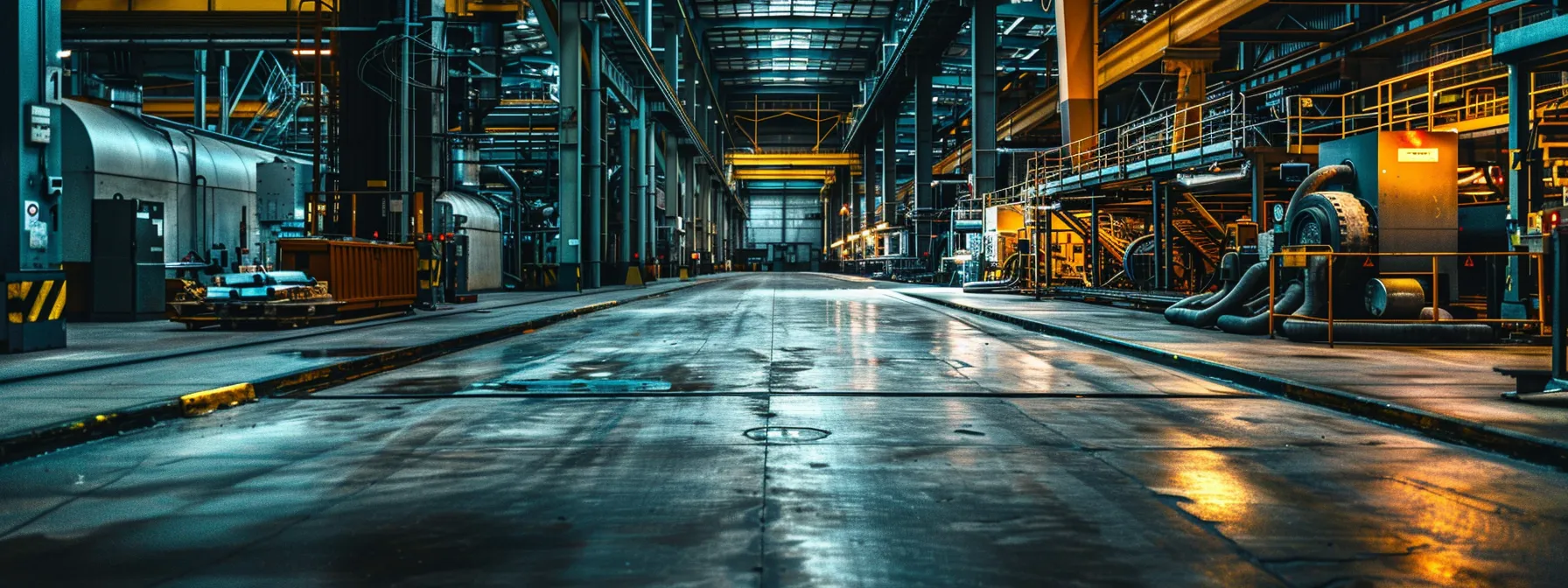
Predictive maintenance is a game-changer in the manufacturing sector, and it is largely driven by the integration of advanced analytics and the IoT. These technologies work together to monitor equipment and predict failures before they happen. This proactive approach to maintenance can save manufacturers significant time and money.
IoT devices collect vast amounts of data from machines on the production floor. When analyzed, this data provides insights into the equipment’s condition, allowing for timely maintenance that can prevent costly downtime. Manufacturers are, therefore, able to schedule repairs during non-production periods, mitigating disruption and maintaining continuous workflow.
Advanced analytics also empower manufacturers to refine their operations further by identifying patterns and trends that might go unnoticed without data-driven analysis. This can lead to process optimizations that enhance the speed and quality of production. Implementing network monitoring software ensures the reliability and security of the IoT infrastructure – a necessity for any operation relying on connected devices.
Adopting Industrial Automation Systems for Efficiency
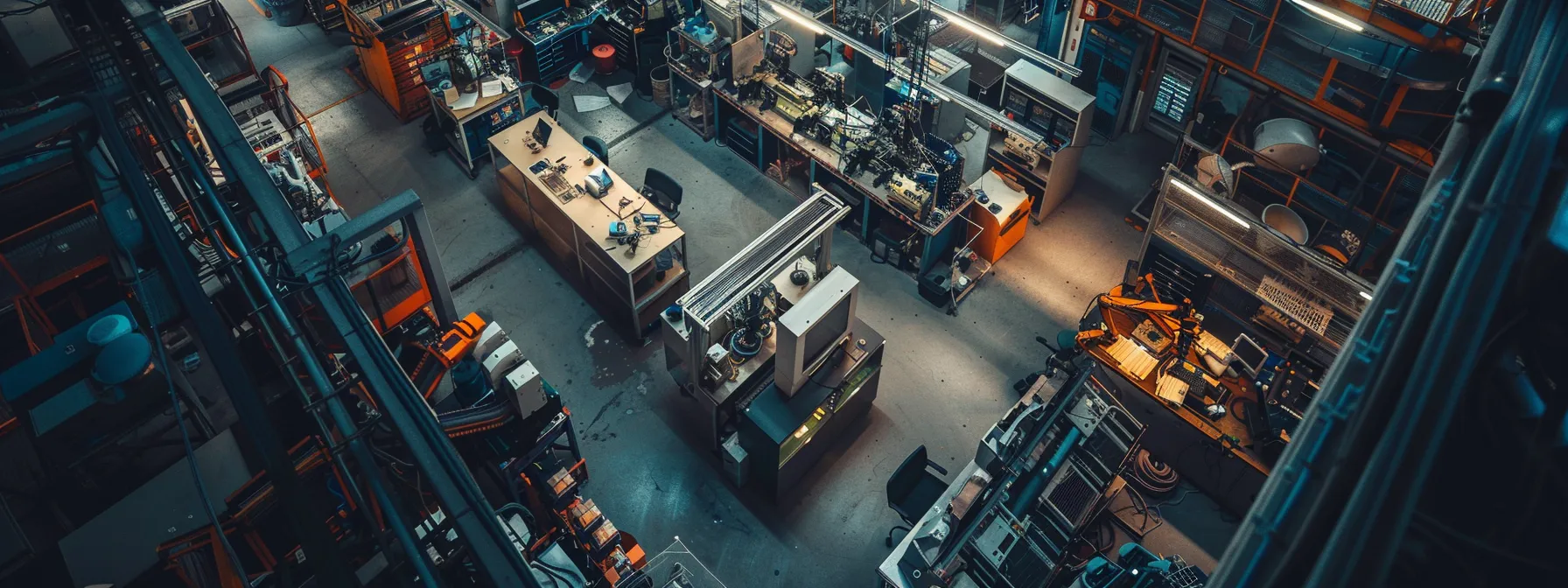
Industrial automation systems extend beyond robotics, encompassing the entire production process. These systems allow for real-time data collection and control over machinery, leading to more refined production methods. By automating tasks, companies can minimize human error and ensure a consistent level of quality across all products.
Scalability is another significant benefit of automation, as it allows manufacturers to adjust production rates according to demand swiftly. This responsiveness can be the difference between capitalizing on market opportunities and falling behind competitors. It also ensures more efficient use of resources, as production can be dialed up or down without substantial changes to staffing or operations.
When implementing automation, companies must consider the disruption it may cause to their current processes. It often requires a period of adjustment and training, which can present challenges. Nevertheless, the long-term benefits, including improved efficiency and lower costs, make it a critical tool for manufacturing success.
Leveraging Additive Manufacturing for Prototyping and Production
Additive manufacturing, or 3D printing, has taken the production of prototypes and finished products to new heights. Its ability to quickly turn digital designs into three-dimensional objects allows for rapid iteration and customization, which is invaluable in a competitive market. This flexibility can significantly shorten the product development cycle, leading to faster time-to-market for new products.
The sustainability aspect of additive manufacturing also cannot be overlooked. By building objects layer by layer, there is often less waste compared to subtractive manufacturing methods that cut away from solid blocks of material. This efficiency is attractive for companies looking to improve their environmental footprint while also cutting costs.
Overall, the successful integration of these advanced manufacturing tools can lead to a significant competitive advantage. From increasing efficiency and reducing waste to enhancing product quality and enabling greater innovation, these tools shape the future of the manufacturing industry. By embracing these technologies, manufacturers can not only meet the challenges of today’s market but set themselves up for continued success in the ever-evolving industrial landscape.